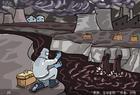
Anellotech is a newly established company that uses bio-based routes to produce aromatics. The company has now obtained a technology license from Amherst University in Massachusetts, USA, and uses CFP technology to produce paraxylene. The CFP technology was invented by Professor George Huber of the University of Massachusetts at Amherst and can use non-food biomass to produce benzene, toluene, xylene, and olefins.
David Suedolski, CEO of Anellotech, said that the CFP technology uses improved zeolite molecular sieve catalysts and fluidized bed reactors to graft catalyst zeolite molecular sieves, widely used in the chemical industry, onto biological raw materials routes.
This process is different from the traditional fermentation process and does not convert cellulose into sugars. Lignocellulosic biomass enters a fluidized bed reactor containing a mixture of catalysts, biomass, and gas, which is pyrolyzed to form pyrolysis vapors, which are then converted to aromatics and olefins as the target products, and carbon monoxide, carbon dioxide, and coke as by-products.
David Sudolsky believes Anellotech will have a cost advantage in producing paraxylene. First, raw materials are non-food biomass such as wood chips and corn stalks, and these raw materials do not require any pretreatment. Second, all chemical reactions occur in one fluidized bed, helping to increase product efficiency. Finally, the improved CFP technology can increase the paraxylene yield to 95%, which greatly reduces the cost of product separation. In addition, process magnification is also relatively simple. "If the cost per ton of dry-based biomass is $50, our paraxylene production costs will be $400 to $600/ton. Together with the favorable conditions of the current green subsidies, I am very optimistic about the outlook for CFP-based xylene. Of course, Ultimately we must compete with petroleum-based paraxylene."
Bio-based para-xylene is one of the most popular research topics in biochemistry in recent years. For example, The Coca-Cola Company has been actively investing in companies and projects in this area. About 30% of the PET bottles currently used by the company are biobased. Since the launch of this bio-based PET bottle in 2009, 10 billion have been sold. Coca-Cola requires bio-based para-xylene to make PET bottles 100% renewable.
bibcock valve,bibcock kitchen taps,bib tap,bibcock valve plastic,brass bibcock valve
Yuyao Gaobao Sanitary Ware Factory , https://www.gurberry.com