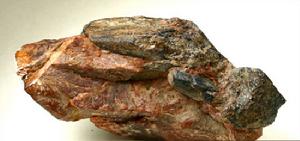
Chromite - Introduction
The chromite chromite is an oxide mineral of chromium and iron. High-carbon ferrochrome (4 to 8% carbon), medium-carbon ferrochrome (0.5 to 4% carbon), low-carbon ferrochrome (0.15 to 0.50% carbon), and micro-carbon ferrochromium (including carbon 0.06%), ultra-micro carbon ferrochromium (containing less than 0.03% carbon), chromium metal, silicon chromium alloy. It's quite hard, black half metallic luster. Chromite is the main source of metallic chromium and can also be used in high temperature refractory materials. Chromite is generally a massive or granular aggregate. The chemical composition of chromite is FeCr2O4, and the crystalline is an equiaxed oxide mineral. The iron in the composition can be partially replaced by magnesium, and when it is mainly Mg, it is called magnesium chromite. With a normal spinel structure. Chromite Cr2O3 content 67.91%. Is the main source of industrial chromium, but also can be made of high temperature refractory materials, such as chrome bricks. Moss hardness 5.5 to 6, the proportion of 3.9 to 4.8. With weak magnetic. Chromite is only produced in ultrabasic or basic rocks. Large chromite deposits are mainly produced in Transvaal in South Africa, near Guilo in Zimbabwe, in the Svidlovsk region of Russia, and in Cuba. China's chromite ore is produced in Tibet, Gansu and Shaanxi.
Chromite - Structural Characteristics
Chromite chemical composition: (Mg, Fe)Cr2O4, the composition is more complex, there are extensively existing Cr2O3, Al2O3, Fe2O3, FeO, MgO five basic components of the isomorphic isotopic displacement.
Characterization: It is characterized by its black, dark brown streak, high hardness and produced in ultramafic rocks; chromite, it looks very much like magnetite, except that it is very weak magnetic and the streak is brown It is different from the black color of magnetite.
Cause of Origin: Magmatic minerals, often produced in ultramafic rocks, symbiotic with olivine; also found in placers.
Famous places of origin: China, Sichuan, Gansu, Tibet, Qinghai, Russia, Cuba, South Pacific French New Caledonia, South Africa, Turkey, Philippines, and Rhodesia.
Name Source: Chromium, Chromitim, from the Greek Chroma, refers to color; this is because all chromium-containing compounds, have a significant color.
Crystal morphology: six octahedral crystals.
Crystal structure: crystal system and space group: equiaxed crystal system, Fd3m; unit cell parameters: a0 = 8.325-8.344 angstroms; powder crystal data: 2.52 (1) 1.46 (0.9) 1.6 (0.9).
Physical properties: Hardness: 5.5-6.5 Specific Gravity: 4.3-4.8 g/cm3 Cleavage: No cleavage Cleavage: Staggered to flat Color: Black streak: Dark brown transparency; Opaque luster: Metal luster. Others: Weak magnetic, high iron content is stronger.
Chromite - raw material characteristics
There are about 50 kinds of chromium-containing minerals that have been discovered in nature by chromite. They belong to oxides, chromates, and silicates. In addition there are a few hydroxides, iodates, nitrides, and compounds. Among them, chromium nitride and chromium oxide are found only in vermiculite. The industrially valuable chromium minerals belong to the chromite spinel minerals. Their chemical formulas are (Mg, Fe2+) (CR, Al, Fe3+)2O4 or (Mg, Fe2+)O (Cr, Al, Fe3+)2O3. Its Cr2O3 content is 18% to 62%.
Chromium minerals with industrial value generally have a Cr2O3 content of more than 30%, of which common ones are:
1. Chromite: The chemical composition is (Mg, Fe)Cr2O4, between ferrous chromite (FeCr2O4, containing FeO32.09%, Cr2O367.91) and magnesium chromite (MgCr2O4, containing MgO20.96%, Cr2O379. Between 04%), it is common to call ferrous chromite and magnesium chromite also chromite. The chromite is an equiaxed crystal system. The crystal is a small octahedron, usually in the form of granular and dense massive aggregates. The color is black, the streak is brown, and the semi-metallic luster has a hardness of 5.5, a specific gravity of 4.2 to 4.8, and weak magnetic properties. Chromite is a magmatic mineral that is produced in ultramafic rocks. When the ore-bearing rocks are weathered and destroyed, the chromite often turns into placer. Chromite is the most important mineral raw material for chromium refining, and iron-rich inferior ore can be used as a high-grade refractory material.
2. Chrome-rich spar: also known as ferrochromium spinel or aluminum chromite. The chemical composition is Fe(Cr,Al)2O4, containing Cr2O32%~38%. Its morphology, physical properties, cause, shape and use are the same as those of chromite.
3. Hard chrome spinel: chemical composition (Mg, Fe) (Cr, Al) 2O4, containing Cr2O332% ~ 50%. Its morphology, physical properties, cause, origin and use are also the same as chromite.
Chromite - Geographical Distribution
The 56 chromite deposits identified by chromite in China have been distributed in 13 provinces, municipalities and autonomous regions across the country. Among them, Tibet is the most, with reserves of 4.251 million tons, accounting for 39.4% of the country's total reserves. Followed by Inner Mongolia, the reserves were 1.744 million tons, accounting for 16.5%; in Xinjiang, the reserves were 1.652 million tons, accounting for 15.3%; and in Gansu, the reserves were 1.496 million tons, accounting for 13.6%. The reserves held by the above four provinces (districts) totaled 9.143 million tons, accounting for 84.8% of the country's total retained reserves. The remaining reserves of Beijing, Qinghai, Hebei, Jilin, Hubei, Shaanxi, Shanxi, Sichuan, and Yunnan provinces (cities, autonomous regions) totaled 1.636 million tons, accounting for only 15.2% of the country's total retained reserves. According to administrative districts, they are mainly concentrated in the southwestern region (4.263 million tons, accounting for 39.6%), the northwestern region (3.706 million tons, accounting for 34.4%), and the North China Region (2.749 million tons, accounting for 25.5%), while the northeast and south-central regions Only 0.5%, East China has not yet identified chromite reserves.
Chromite - Smelting process
Ferrochromium smelting Ferrochromium is an iron alloy consisting of chromium and iron and is an important alloying additive for steelmaking. The chromite used for the smelting of ferrochromium typically requires 340 to 50% Cr2O3 and a ratio of chromium to iron of more than 2.8. In recent years, mass-produced 50% chromium-containing "charge grade ferrochromium" uses ores with lower ratios of Cr2O3 and chromium to iron.
Ferrochromium is divided into carbon ferrochromium (including loading grade ferrochromium), medium carbon ferrochromium, low carbon ferrochrome, micro-carbon ferrochrome and so on according to different carbon content. Commonly used silicon chromium alloy, chromium nitride iron and so on. Ferrochromium is mainly used as an alloy additive for steelmaking. It was added in the late stage of steelmaking refining. In the smelting of low-carbon steels such as stainless steel, low- and micro-carbon ferrochromium must be used, so that the production of refined ferrochromium was once more developed. Due to the improvement of the steelmaking process, when stainless steels and other steels are produced by the AOD method (see External Refining), the furnaces are filled with carbon ferrochromium (mainly loaded grade ferrochromium). Micro-carbon ferrochromes adjust the composition, so now the focus of ferrochromium production is to refine carbon ferrochromium.
The carbon ferrochrome is smelted in a reducing furnace, using coke as a reducing agent, and silica or bauxite as a flux. The slag composition is generally SiO227 to 33%, MgO 30 to 34%, Al2O 326 to 30%, and Cr2O3 <9.0%. Due to the formation of chromium carbide, the product contains 4 to 9% carbon. Modern smelting ferrochrome reduction furnace capacity of 10000 ~ 48000 kVA, generally closed fixed type, smelting power consumption 3000 ~ 4000 kwh • hours / ton. The electric furnace for smelting silicon-chromium alloy is similar to the ferrochrome reduction electric furnace. The smelting method includes one-step method and two-step method. One-step smelting with chromite, silica, coke and flux. The two-step method adopts carbon-free ferrochrome, silica, and coke as raw materials for slag-free smelting, and the smelting process is generally similar to ferrosilicon production. Smelting electricity consumption is about 3000 to 4000 kWh per ton.
Medium, low, and micro-carbon ferrochromium are generally made of silicon-chromium alloy, chromite, and lime as raw materials, refined and desiliconized using a 1500-6000 kVA electric furnace, and operated with high alkalinity slag (CaO/SiO2 is 1.6-1.8). Low- and micro-carbon ferrochromes have also been produced on a large scale using thermal loading. Two electric furnaces are used in the production, one furnace smelts silicon-chromium alloy, and one furnace melts slag consisting of chrome ore and lime. The refining reaction is carried out in two stages in two stages: 1 After the molten slag in the slag furnace is injected into the first ladle, the silicon-chromium alloy in the other ladle, which has been initially desiliconized, is mixed in due to the excess slag oxidizing agent. A large amount of desiliconization is sufficient to obtain micro-carbon ferrochromium with less than 0.8% silicon and 0.02% carbon. 2 After the reacted slag (containing about 15% of Cr2O3) in the first ladle was transferred to the second ladle, the silicon-chromium alloy (silicon-containing 45%) smelted in the silicon-chromium furnace was hot-divided into the residue and reacted. After the initial desiliconization of silicon-chromium alloy (containing about 25% of silicon), into the first barrel further desiliconization, slag containing Cr2O3 less than 2 to 3% can be discarded.
Oxygen is used to refine medium- and low-carbon ferrochromium using liquid carbon ferrochrome as a raw material. During blowing, a small amount of lime and fluorspar are added to the bath to form a slag. Before the tapping, silicon-chromium alloy or ferrosilicon is added to recover the slag. chromium. Micro-carbon ferrochrome blowing is only possible under a certain degree of vacuum.
Vacuum solid-state decarburization refining, using finely ground high-carbon ferrochrome as raw material, in which a part of the fined high-carbon ferrochrome is oxidized and roasted as an oxidant, added with water glass or other binders, pressed into agglomerates, and then cooled After drying, it can be heated and reduced for 35-50 hours under a vacuum of 0.5-10mmHg at a temperature of 1300-1400°C in a vacuum furnace under a car to obtain microcarbons containing less than 0.03% or even less than 0.01% of carbon. Ferrochrome.
Chromium is introduced into iron, steel, and many superalloys through an intermediate medium: the chrome iron alloy is fused. The method is pyrometallurgical reduction of chromite ore with carbon and/or silicon in high temperature arc furnaces. Ferrochromium alloys are essentially an alloy of iron and chromium and artificially add a significant amount of carbon and silicon.
Chromite - A Brief History of Mining
The chromium element of chromite was discovered by French chemist Faulklin in 1798. The chromite ore was first discovered in Russia's Ural Mountains in 1799. The discovery and development of this ore became the main source of supply for the world's chromite ore in the 18th century, when chromium was mainly used in the chemical industry. After the chromite was discovered in Maryland in the United States in 1827, chromite was discovered in Pennsylvania and Virginia, which made the United States one of the world's limited suppliers of chromite. In 1860 Turkey discovered a large deposit for the international market. Until the discovery of chromium ore in India and Rhodesia in 1906, Turkey has been the main source of chromite ore supply. So far, more than 40 countries and regions in the world have discovered chromite, with a total reserve of 3.7 billion tons and a production volume of more than 10 million tons.
Although China had discovered traces of chromite in Jilin, Ningxia, and Hebei before 1949, it did not conduct in-depth investigations and studies. The country only knows about 2 ore points, one is Kaishan Mountain in Jilin, and the other is For Ningxia Xiao Songshan, the former has been plundered by Japanese invaders. After the founding of New China, due to the needs of industrial development, the search and exploration of chromite started. At the beginning of the 1950s, the Northeast Heavy Industry Group team went to Kaishantun and the Geological Team to work in Xiaoshan Mountain in Ningxia and Gaositai and Damiao in Hebei Province. In the 1960s, chromite surveys were conducted in Miyun, Beijing and Subei, Gansu Province. Finally, the gamma iron ore in the Sendai, Miyun County and the Erji chromite ore in the Subei region were discovered. However, the real breakthrough of China's chromite resources should be said to be after chromite found in Xinjiang and Tibet. The chromite work in Xinjiang was carried out in the late 1950s. When the radioactivity was measured in 1958, the Saltohai chromite ore was discovered. In 1959-1964, the whale chromite ore was found by gravity, magnetism and drilling methods. From 1964 to 1966, the Department of Geology organized a battle in Xinjiang. In 1970, the whale mine was completed and put into production. This was the only chromite ore mine developed by the formal well construction. The chromite from Tibet was discovered in the late 1950s and early 1960s. After years of work, the largest chromite ore deposit, the Luobusa chromite ore, was discovered, and Tibet became the main source of chromite.
Chromite - Resource Status
Chromite Ore As of the end of 1996, a total of 56 chromite ore deposits were discovered in China, and the total proven chromite ore reserves were 13.149 million tons, of which A+B+C grades accounted for 43%, which was 5.652 million tons. Excluding the mining and loss over the years, the reserve of chromite ore was 10.779 million tons, of which the A+B+C class accounted for 34%, which was 3.684 million tons. The increase in reserves of chromite is still very rapid. Accumulated proved reserves in 1957 were only 181,000 tons. It increased to 2.233 million tons in 1965, 11.907 million tons in 1985, and 13.149 million tons in 19996. The total amount of chromite resources is 44 million tons and the resource potential is 31 million tons. In 1995, the world reserves of chromite ore were 3.7 billion tons, and the reserve base was 7.4 billion tons, which was mainly concentrated in South Africa (3 billion tons of reserves, 5.5 billion tons of reserves) and Zimbabwe (140 million tons of reserves and 9.3 billion tons of reserves). Kazakhstan (320 million tons of reserves, 320 million tons of reserves), Russia (4 million tons of reserves, 460 million tons of reserves), and other countries with more reserves are also Finland, India, Brazil, Turkey, etc. (Table 3.4.2) ). If the A+B+C reserves are compared with the reserve base of these countries, China is far behind them.
1. The deposit is small and scattered
At present, no large-scale chromite deposits with reserves greater than 5 million tons have been discovered, and only 4 medium-sized deposits with reserves exceeding 1 million tons have been found. They are the Luobusha in Tibet, Erji Boulevard in Gansu, and Saltohai in Xinjiang. Inner Mongolia's Hegenshan (3756 mine). The rest are all small deposits with reserves of less than 1 million tons. It is the Robusha deposit with the largest reserves. The reserves of 3.96 million tons are distributed in more than 100 ore bodies of 7 ore groups. The largest ore body is only 325 meters long.
2. Uneven distribution area, poor development and utilization conditions
As mentioned above, 84.8% of the retained reserves of chromite deposits are distributed in these remote provinces (regions) such as Tibet, Xinjiang, Gansu, and Inner Mongolia. The transportation lines are long and the traffic is inconvenient.
3. Poor mines and rich ore reserves generally account for about half
Among the reserves, 46.3% (4.993 million tons) of ore reserves and 53.7% (578.6 million tons) of rich mines are in reserve. The bonanza is mainly distributed in Tibet and Xinjiang, accounting for 73.5% and 13.8% of the total bonanza. From a use perspective, metallurgical-level reserves accounted for 37.4% of total reserves, chemical-grade reserves accounted for 38.4%, and refractory-grade reserves accounted for 24.2%.
4. There are few open pits and small, easy-to-professional chromium-rich iron ore has been mined
Only about 6% of the chromite reserves are suitable for individual exposure, and most of them require pit mining. Some small, rich and easily mined chromite ore has been harvested. The whale like Xinjiang and the Dongqiao chromite from Tibet were closed in 1983 and 1982, respectively. The former produced 310,000 tons of chromite. The people produced 176,300 tons.
5. Single genetic type of deposit
The currently known chromite deposits are mainly late magmatic deposits. However, some of the world's famous large-scale and superlarge magmatic early segregation deposits with layered features have not yet been developed in China.
Chromite - Industrial Applications
Chromite is one of the important strategic materials for metallurgical chromium. Due to its characteristics of hardness, wear resistance, high temperature resistance and corrosion resistance, it has been widely used in the metallurgical industry, refractory materials and chemical industry. In the metallurgical industry, chromite is mainly used to produce ferrochromium and metallic chromium. Chromium-iron alloys are used as steel additives to produce a variety of high-strength, corrosion-resistant, wear-resistant, high-temperature, oxidation-resistant special steels, such as stainless steel, acid-resistant steel, heat-resistant steel, ball-bearing steel, spring steel, and tool steel. Chromium metal is mainly used for the smelting of special alloys with elements such as cobalt, nickel, and tungsten. These special steels and special alloys are indispensable materials for aerospace, aerospace, automotive, shipbuilding, and defense industries to produce *guns, **, rockets, ships, and so on. In refractories, chromite is used to make chrome bricks, chromium-magnesite bricks and other special refractories. Chromite is mainly used in the chemical industry to produce ****, and then take other chromium compounds for pigment, textile, electroplating, tanning and other industries, but also the production of catalysts and catalysts. Chromite is a shortage of minerals in China, with low reserves and low production. More than 80% of the annual consumption depends on imports. Chromium ore is an indispensable mineral resource for the development of metallurgy, defense, and chemical industries. It is mainly used in the metallurgical industry to produce stainless steel and various alloy steels, alloys, glass, ceramics, and refractory materials.
Headlights,Cob Led Headlight,Led Aluminium Alloy Headlamp,7Led Plastic Headlight
NINGBO ZHENGUO INTELLINGENT LIGHTING CO.,LTD , https://www.zguolight.com