
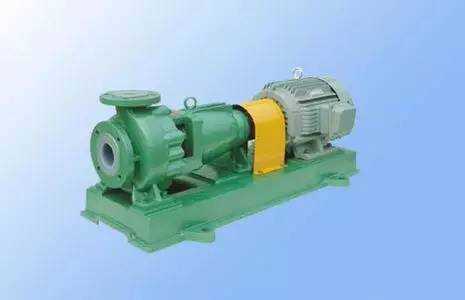
1. What is a chemical centrifugal pump?
A: It uses the impeller to subject the liquid flowing through the impeller to centrifugal force, which increases the mechanical energy of the liquid and thus transports the liquid. It is a machine that increases the energy of the liquid.
2. What are the characteristics of chemical centrifugal pumps?
Answer: 1) can adapt to chemical process needs; 2) corrosion resistance; 3) high temperature and low temperature resistance; 4) wear resistance and erosion resistance; 5) reliable operation; 6) no leakage or less leakage; Liquid.
3. What kinds of chemical pumps are classified according to working principle and structure?
A: According to the working principle, it can be divided into: vane pump, positive displacement pump and other types of pumps: electromagnetic pump that uses electromagnetic energy to transport liquid electric conductor state; pump that uses fluid energy to transport liquid, such as jet pump, air lifter, etc.
4. What is the working principle of the centrifugal pump?
Answer: The drive machine rotates the impeller, and the blades in the impeller drive the fluid to rotate together to generate centrifugal force. Under the centrifugal force, the fluid is swept along the blade flow path to the impeller outlet, through the diffuser, and the volute is fed. Export pipe. When the impeller rotates continuously, the fluid is continuously sucked in and discharged, so that the centrifugal pump operates continuously.
5. What are the advantages of a centrifugal pump?
Answer: 1) The output of single unit is large and continuous, no pulse, and the operation is stable;
2) The pump has small size, light weight, less floor space and low investment;
3) The equipment structure is simple, the wearing parts are few, the Yunzhuang period is long, and the operation and maintenance workload is small;
4) Good adjustment performance and reliable operation;
5) The inside of the pump does not need lubrication, and the delivered fluid will not be contaminated by lubricating oil.
6. What is the flow rate of the centrifugal pump?
Answer: The flow rate of the centrifugal pump refers to the amount of liquid discharged from the discharge port of the pump per unit time.
7. How many expressions are there for centrifugal pump flow?
A: Centrifugal pump flow has two forms of expression: volume flow and mass flow.
8. What is volume flow?
A: Volume flow (Qv) refers to the volume of liquid discharged from the discharge port of the pump per unit time, in m3/s.
9. What is mass flow?
Answer: The mass flow rate (Qm) refers to the mass of liquid discharged from the discharge port of the pump per unit time, and the unit is kg/s.
10. What is the relationship between volumetric flow and mass flow of a centrifugal pump?
Answer: The volumetric flow rate and mass flow rate of the centrifugal pump are both expressions of the flow rate. The relationship between the two is: Qm=QvÏ (Qm is the mass flow rate kg/s; Qv is the volume flow rate m3/sÏ is the density of the liquid, kg/ M3).
11, what is the lift of the centrifugal pump?
Answer: The head (indenter) of the pump refers to the increase in energy per unit mass of liquid flowing through the pump, also known as the effective energy head, in m.
12. What are the lifts of the centrifugal pump?
A: The lift is an energy unit that can be expressed by the height of the liquid column that pumps the liquid. It includes liquid potential energy, static pressure energy, and kinetic energy.
13. What are the factors related to the lift of the centrifugal pump?
Answer: The theoretical head and speed of the pump, the angle at which the blade exits, the number of blades, and the flow rate of the pump are related.
14. How is the level of A Yang in continuous protection determined?
Answer: 1) The larger the blade exit angle is, the theoretical head increases with the increase of flow rate, and the smaller the blade exit angle, the theoretical head decreases with the increase of flow.
2) The more the number of blades, the larger the theoretical head.
3) The higher the number of revolutions, the larger the theoretical head.
15. What is the speed of the centrifugal pump?
Answer: The rotation speed of the centrifugal pump refers to the number of working times of the centrifugal pump rotor per unit time, and its unit is r/min.
16. What is the power of the centrifugal pump?
Answer: The power of the pump usually refers to the work transmitted from the prime mover to the pump shaft per unit time, also known as the shaft power, in units of W or KW.
17. What is the effective power of the centrifugal pump?
A: It is the effective energy obtained by outputting liquid from the pump per unit time, also known as output power, in units of W or KW.
18. What is the efficiency of a centrifugal pump?
A: The efficiency of the pump is the ratio of effective power to shaft power, which reflects the extent of energy loss in the pump.
19. What is the hydraulic loss of a centrifugal pump?
A: The hydraulic loss of a centrifugal pump is also called the flow loss, which is the difference between the theoretical head and the actual head.
20. What are the hydraulic losses of a centrifugal pump?
A: The hydraulic loss of a centrifugal pump includes three aspects: eddy current loss, resistance loss loss, and impact loss.
21. What is the volume loss of the centrifugal pump?
A: Volume loss is the energy loss caused by flow leakage.
22. What is the mechanical loss of the centrifugal pump?
A: Mechanical losses are due to wear on the bearings, seal packing, and wear on both sides of the impeller.
23. After the centrifugal pump changes the number of revolutions, what changes in the head, flow, and shaft power?
Answer: After the centrifugal pump changes the number of revolutions, its head, flow rate and shaft power also change. If the medium delivered by the pump is not changed, the flow ratio is higher than the speed ratio, the head ratio is equal to the square of the speed ratio, and the shaft power ratio is equal to the speed. Than the cube.
24. How to adjust the working point of the centrifugal pump?
Answer: 1) Adjust the adjustment of the performance of the pipeline system: (1) adjust the discharge valve; (2) bypass the method.
2) Adjust the pump performance adjustment method: (1) change the pump speed; (2) change the impeller diameter; (3) change the impeller level.
25. What is the suction height of the centrifugal pump?
A: The suction height of the pump refers to the height from the liquid suction surface to the center line of the pump inlet, that is, the installation height.
26. What is the relationship between the suction height of the centrifugal pump and the temperature?
Answer: The higher the temperature of the liquid, the larger the saturated vapor pressure and the smaller the suction height, the more likely the pump will cavitation, so the medium over temperature is not allowed during the pump operation.
27. What is the cavitation phenomenon of a centrifugal pump?
Answer: The phenomenon that the liquid is vaporized, condensed, and impacted to form high pressure, high temperature, high frequency impact load, causing mechanical peeling and electrochemical corrosion damage of metal materials is called cavitation.
28. How to improve the cavitation resistance of centrifugal pumps?
Answer: The measures to improve the cavitation resistance of the centrifugal pump are: 1) measures to improve the cavitation resistance of the centrifugal pump itself; 2) measures to improve the effective cavitation allowance of the inlet device.
29. What are the measures to improve the effective cavitation allowance of the liquid inlet device?
Answer: (1) increase the pressure of the liquid in the liquid storage tank before the pump to increase the effective cavitation allowance; (2) reduce the installation height of the pump of the suction device; (3) change the suction device to the reverse irrigation device; (4) Reduce the flow loss on the pipeline before the pump.
30. What are the factors that allow the suction vacuum of the pump to be related?
Answer: 1) saturated vapor pressure of the liquid to be transported; 2) diameter of the low pressure zone of the impeller; 3) density of the liquid; 4) rotational speed of the pump; 5) local atmospheric pressure; 6) temperature of the liquid.
31. What is the role of the centrifugal pump impeller?
A: The impeller is the heart of the centrifugal pump. It is the most important part of the centrifugal pump. It is the main body for the fluid to be transported. It applies mechanical energy to the fluid, increases the pressure and kinetic energy of the fluid, and completes the process of transporting the fluid.
32. Where is the most prone to cavitation in centrifugal pumps?
Answer: 1) The front cover with the largest curvature of the impeller is close to the low pressure side of the inlet edge of the blade;
2) in the extrusion chamber, the volute tongue and the vane are near the low pressure side of the inlet edge;
3) a sealing gap between the outer tip of the blade of the high specific speed impeller without the front cover and the casing and the low pressure side of the blade tip;
4) The first stage impeller in the multistage pump.
33. Why can't I install the centrifugal pump too high from the ground?
Answer: When installing the centrifugal pump, the installation height must be within the allowable installation height. If the centrifugal pump is too high from the ground, the effective cavitation allowance of the liquid is reduced. When the liquid enters the low pressure zone of the pump, the pressure is lower than the liquid delivery temperature. Saturated vapor pressure, the liquid boils and vaporizes, causing cavitation and causing damage to the pump itself.
34. What are the components of the centrifugal pump impeller?
A: The impeller includes: blades, front cover, rear cover, and hub. Some impeller rear cover has balance holes, and some impellers have induction wheels on the front.
35. Which order can the impeller be in the order of the specific number of revolutions and the direction in which the fluid flows in the impeller?
A: It can be divided into radial flow impeller, mixed flow impeller, oblique flow impeller and axial flow impeller.
36. What is a closed impeller?
A: The impeller with front and rear covers is called a closed impeller. Such an impeller forms a completely closed flow passage, has a high lift head and high hydraulic efficiency, and is widely used in a fluid medium without impurities in chemical plants.
37. What is an open impeller?
A: There is no front cover, the rear cover is small in size, and the impeller whose blade is completely exposed is called an open impeller.
38. What kind of occasion is the open impeller generally used for?
Answer: Open impeller is generally used to transport slurry, and liquid with large viscosity or solid particle suspension, which is not easy to block, but liquid is easy to reverse between the blades, so the lift and efficiency are also high, and some are added before the impeller. The induction wheel is used in a high speed centrifugal pump.
39. What is a semi-open impeller?
A: Only the impeller of the rear cover is called a semi-open impeller. Its efficiency is between the closed impeller and the open impeller, which can be used in high-speed pumps, and the induction wheel can be installed in front of the impeller. It can be used in axial pumps with lower lift or in mud pumps.
40. What is the number of blades of the centrifugal pump impeller?
Answer: The number of blades of the centrifugal pump impeller is usually 6-8 pieces. For the centrifugal pump with liquid containing impurities, the number of blades is small, which is as small as 2~4 pieces, and the shape of the blade also changes significantly. The diameter of the pump, the larger the flow rate, the more the blades, the higher the specific number of revolutions, the fewer the number of blades.
41. What kind of material is the impeller of the centrifugal pump?
A: Commonly used materials are: gray cast iron, acid-resistant ferrosilicon, alkali-resistant aluminum cast iron, chromium-based stainless steel, chromium-manganese-nitrogen series acid-resistant cast steel, chromium-manganese-nitrogen series alkali-resistant cast steel, hard lead, nickel-containing acid-resistant cast steel, Cr18 , copper alloy, aluminum-magnesium alloy, etc.
42. What are the material requirements for manufacturing centrifugal pump impellers?
A: There is sufficient strength and rigidity, good welding or machining performance. For chemical pumps, it also needs to be resistant to liquid medium corrosion and cavitation.
43. What is the function of the pump body of the centrifugal pump?
Answer: The liquid gradually decreases in the channel, and a part of the kinetic energy is converted into static pressure energy, which not only increases the pressure of the liquid, but also reduces the energy loss inside the pump body caused by the passage being too large. Therefore, the pump body collects liquid as both the outer casing of the pump, and it is itself an energy conversion device.
44. What are the common structures of the pump body?
Answer: The pump body is the center of the pump structure, also called the volute or pump casing. The forms are: horizontal split type, vertical split type, inclined split type, simplified type.
45. According to the support form of the pump casing, which ones can be divided into?
A: According to the support form of the pump casing, it can be divided into standard support type, center support type, cantilever type, pipeline type and hanging type.
46. ​​Why does the centrifugal pump generate axial force?
Answer: Because the pressure of the suction and discharge ports is not equal, the hydraulic forces on both sides of the impeller are not completely symmetrical, resulting in axial force.
47. What is the hazard of the axial force of the centrifugal pump?
Answer: Due to the existence of unbalanced axial force, the work load of the thrust bearing is aggravated, which is unfavorable for the work that will go out. At the same time, the axial force causes the whole rotor of the pump to sway to the suction port, causing vibration and impeller inlet and seal. The ring is rubbed, and when it is serious, it does not work properly.
48. How to eliminate the axial force of the centrifugal pump?
Answer: 1) open balance hole; 2) add balance tube; 3) install balance vane; 4) use double suction impeller; 5) symmetric arrangement of impeller; 6) use balance disc.
49. What is the shaft seal?
A: The seal between the rotating pump shaft and the fixed pump casing is called a shaft seal.
50, what is the role of shaft seal?
Answer: The function of the shaft seal is to prevent high-pressure liquid from leaking out from the pump along the shaft, or the outside air is infiltrated along the shaft. For the shaft seal of the centrifugal pump, it is a dynamic seal.
51, what is the packing seal?
A: The packing seal is a traditional gland seal. It relies on the gland to create a pre-tightening force, thereby compressing the packing, forcing the packing to press against the sealing surface (the outer surface of the shaft and the sealing cavity), creating a radial force for the sealing effect, thereby sealing.
52, what are the characteristics of the packing seal?
Answer: The packing seal can be applied to large stuffing boxes and heavy loads. The structure is simple, the operation and maintenance are convenient, and the cost is low. The disadvantage is that the power consumption is large, the sealing reliability is poor, and the shaft seal is worn during use.
53. What is the material used for packing seals?
Answer: 1) synthetic fiber plus polytetrafluoroethylene; 2) synthetic fiber; 3) fiber plus black lead; 4) polytetrafluoroethylene; 5) hemp PTFE; 6) asbestos immersion PTFE; 7) asbestos graphite; 8) Asbestos plus black lead; 9) cotton plus natural rubber.
54, what is a mechanical seal?
Answer: Mechanical seal is also called end seal. It is a shaft seal device for rotating machinery. It refers to the cooperation of at least one pair of end faces perpendicular to the axis of rotation under the action of liquid pressure and compensating mechanism elastic force (or magnetic force) and auxiliary seal. A device for preventing fluid leakage caused by sticking and sliding relative to each other.
55. What is the working state of the dynamic ring, static ring, sealing ring and elastic component of the mechanical seal?
Answer: 1) dynamic seal ring (also known as moving ring); 2) static seal ring (also known as static ring); 3) static ring seal ring; 4) moving ring seal ring; 5) elastic element.
56. What are the selection conditions for common fillers?
Answer: In the chemical plant, the selection of pump packing should meet the following four requirements: the packing can resist medium corrosion; the packing has certain strength; the packing has certain homogeneity and plasticity; the packing can adapt to the temperature of the medium (high temperature or low temperature).
57. What is a mechanical seal?
Answer: Mechanical seal is also called end seal. It is a shaft seal device for rotating machinery. It refers to the cooperation of at least one pair of end faces perpendicular to the axis of rotation under the action of liquid pressure and compensating mechanism elastic force (or magnetic force) and auxiliary seal. A device for preventing fluid leakage caused by sticking and sliding relative to each other.
58. What is the role of mechanical seals?
A: Its main function is to change the leaky axial seal to a more difficult to leak end face seal.
59. What are the components of the mechanical seal?
Answer: The mechanical seal includes a seal ring, a static seal ring, a spring load device and a static sealing element.
60, what are the advantages of mechanical seal?
Answer: 1) reliable sealing; 2) long life; 3) low friction power consumption; 4) vibration axis of the rotating shaft is not sensitive to the deflection of the housing hole; 5) wide application range.
61. What are the disadvantages of mechanical seals?
Answer: The mechanical seal structure is complicated to manufacture, the dynamic and static end face processing requirements are high, the friction pair load other component materials are not easy to match, and at the same time, certain installation technology is required, and the cost is high.
62. Why should the mechanical seal be washed?
Answer: The sealing medium in the sealed cavity contains particles and impurities, which must be re-returned. Otherwise, due to the precipitation of crystals, the deposition of particles and impurities, the mechanical seal static and dynamic ring loses its floating property and the spring fails. More serious is the particles, impurities entering the friction pair will aggravate the friction and wear, and the rapid destruction of the child's mechanical seal.
63. How many methods are used for mechanical seal washing?
Answer: 1) Self-rinsing; 2) External flushing; 3) Backflushing.
64. What is the relationship between the sealing performance of the mechanical seal and the service life?
Answer: The sealing performance of the mechanical seal has a service life, which is related to the material of each component, especially the material of the end seal (friction pair), and the material of the auxiliary seal material.
65. What are the materials used for the end face seal friction pair?
Answer: The materials used for the end face seal friction pair are graphite, ceramic, hardfacing hard alloy, tungsten carbide alloy.
66. What are the materials used for the auxiliary seals?
A: The material used for the auxiliary seal is rubber, PTFE.
67. What are the materials used for the elastic components?
Answer: The materials used for the elastic components are spring material and bellows material.
68. What are the faults on the parts of the mechanical seal?
Answer: 1) Failure of seal end face: wear, hot crack, deformation, damage; 2) failure of spring: slack, breakage and corrosion; 3) failure of auxiliary seal: assembly failure has block, crack, bruise , crimping and twisting; non-assembled faults are deformed, hardened, cracked and deteriorated.
69. What is the function of the shaft of the centrifugal pump?
Answer: The function of the pump shaft is to support the rotating parts such as the impeller, and drive the impeller to take the high-speed rotating screen to transmit the driving power component in the determined working position.
70, what is a sliding bearing?
Answer: Bearings that use the sliding motion of the shaft and the bearing to bear the load are called plain bearings.
71. Can sliding bearings be divided into several categories?
Answer: According to the principle of oil film formation between the two opposite moving surfaces of the sliding bearing, it can be divided into fluid dynamic pressure lubrication bearing (also known as dynamic pressure bearing) and hydrostatic bearing (also known as hydrostatic bearing).
72. What are the commonly used bearing materials?
Answer: 1) cast iron; 2) bearing alloy; 3) copper alloy; 4) aluminum alloy; 5) ceramic metal; 6) graphite; 7) other non-metallic materials: rubber, phenolic tape, nylon.
73. What is a rolling bearing?
A: Bearings that use rolling friction to withstand loads are called rolling bearings.
74. What are the components of the rolling bearing?
Answer: 1) inner ring (also known as inner or inner ring); 2) outer ring (also known as outer casing or outer ring); 3) rolling element (steel ball or roller); 4) cage (also known as retainer) And isolators).
75. What is the role of the inner ring of the rolling bearing?
A: The inner ring (also known as the inner or inner ring) is usually fixed to the journal and the inner ring rotates with the shaft. The outer surface of the inner ring has a groove for rolling a steel ball or a roller, which is called an inner groove or an inner race.
76. What is the role of the outer ring of the rolling bearing?
A: The outer ring (also known as the outer casing or outer ring) is usually fixed to the housing of the bearing housing or machine to support the rolling elements. The outer surface of the outer ring has grooves for rolling steel balls or rollers, called outer grooves or outer races.
77. What is the role of rolling bearing rolling elements?
Answer: Each set of rolling elements (steel balls or rollers) is equipped with one or several sets of rolling elements, which are installed between the inner ring and the outer ring to play the role of rolling and transmitting force. The rolling element is a load-bearing part whose shape, size and number determine the bearing's ability to withstand loads and high-speed operation.
78. What is the role of the rolling bearing cage?
A: The cage (also known as the retainer and the isolator) separates the rolling elements in the bearing evenly from each other, so that each rolling element rolls normally between the inner ring and the outer ring. In addition, the cage has the function of guiding the rolling body movement, improving the lubrication conditions inside the bearing, and preventing the rolling elements from falling off.
79. What are the basic requirements for steel for rolling bearings?
Answer: 1) high contact fatigue strength; 2) good wear resistance; 3) hardness generally reaches HRC 61-65. ; 4) good anti-rust performance; 5) good processing performance.
80. What is the play?
A: The so-called rolling bearing clearance is the maximum amount of movement of a ferrule in the radial or axial direction.
81. What is radial clearance?
A: The maximum amount of activity in the radial direction is called the radial clearance.
82. What is the axial clearance?
A: The maximum amount of activity along the axial direction is called the axial clearance.
83. What kinds of clearance can be divided into?
Answer: According to the state of the bearing, the clearance can be divided into the following three types: original clearance, installation clearance, and working clearance.
84. What is the inspection method for radial clearance?
Answer: 1) Feeling method: This method is dedicated to single row radial ball bearings.
2) Measurement method: (1) check with a feeler gauge; (2) check with a dial gauge.
85. What are the common faults of rolling bearings?
Answer: 1) the bearing becomes blue or black; 2) the support heats up too fast; 3) the noise is abnormal during operation; 4) the rolling element is seriously worn; 5) the raceway has pits; 6) the inner and outer rings of the bearing have cracks; ) The bearing metal is peeled off; 8) The rolling element is crushed and appears in the thrust bearing; 9) The hand does not move after installation; 10) The bearing raceway produces scratches.
86. What are the methods for measuring the clearance of a centrifugal pump?
Answer: 1) pressure lead wire method; 2) bar inspection method; 3) lifting axis method; 4) measuring method; 5) feeler method.
87. How many methods for measuring the back interference of bearings?
Answer: The measurement method of the back interference of the bearing is the lead wire method and the measuring method.
88. What is the technical standard for repairing the labyrinth seal oil ring of centrifugal pump?
Answer: Check the sealing teeth at all levels, there should be no defects such as dirt, rust, burrs, cracks, bends, notch deformation and breakage. Seal damage and gap should be replaced when there is excessive gap. There should be no loose or too tight after sealing assembly, seal The tip of the tooth should be sharp.
89. When repairing a centrifugal pump, what technical standards should the impeller meet?
Answer: 1) The bushing outer garden, the balance disk hub bounce must not exceed 0.08mm;
2) impeller seal ring, hub, bearing end face, balance disk hub axial runout should be less than 0.10mm;
3) The impeller and the shaft are matched with H7/h6.
4) If necessary, the impeller should find a static balance.
90. What are the precautions when disassembling the chemical pump?
Answer: First, correct disassembly; second, cleaning, inspection, repair or replacement of parts; third, careful assembly according to technical requirements; fourth, reasonable position between components after assembly and reasonable adjustment of gaps between components.
91. Why is the centrifugal pump pumped out?
Answer: There is no pump before the centrifugal pump starts, the air is ingested, the liquid is not full or the medium is vaporized a lot. This is the centrifugal pump outlet pressure which drops sharply and fluctuates drastically. This phenomenon is called evacuation.
92. Where is the centrifugal pump pumping out?
A: The performance is that the outlet pressure tends to zero or close to the inlet pressure of the pump. The friction pair of the contact parts in the pump and the mechanical seal is worn out due to dry friction or semi-dry friction.
93. How to prevent the centrifugal pump from being pumped out in mechanical terms?
A: In terms of machinery, it is mainly to do a good job of sealing management. It is strictly forbidden to let air enter the medium from pipelines and pumps. Strictly check the static and dynamic seals during maintenance to prevent leakage due to equipment.
94. Why does the liquid in the centrifugal pump vaporize?
Answer: When the centrifugal pump is running, the liquid pressure drops along the pump inlet to the impeller inlet. At the K point near the inlet of the vane, the liquid pressure pK is the lowest. Thereafter, as the impeller works on the liquid, the liquid pressure rises rapidly. When the pressure near the impeller vane inlet is less than the saturated vapor pressure at the liquid delivery temperature, the liquid vaporizes.
95. What are the factors related to the centrifugal pump evaporation?
A: It has a relationship with the liquid and the pump itself. It is related to the saturated vapor pressure and vapor pressure of the medium at the current temperature, and also related to the cavitation allowance of the pump. The higher the saturated vapor pressure, the easier the medium is to vaporize. The greater the amount of erosion, the less easily the liquid vaporizes.
96. What is the reason for the high current of the centrifugal pump motor?
Answer: 1) The relative density and viscosity of the process medium exceed the index; 2) Electrical fault; 3) The outlet valve is fully open when the pump starts, the resistance inside the outlet pipe is too small; 4) The balance pipe is not smooth; 5) The pump assembly is not good, the movement is static Partially rubbed or stuck.
97. What is the NPSH of the centrifugal pump?
A: NPSH is the abbreviation of Net Positive Suction Head. It is literally translated as a net positive suction head. It is customary in China to be called cavitation allowance. He refers to the energy of the liquid at the impeller inlet (relative to the reference surface) that exceeds the saturated vapor pressure at that temperature, as determined by the pump installation conditions. Expressed in the form of a water head. The unit is m.
98. What is the reason why the centrifugal pump is not in operation?
Answer: 1) There is air in the pump or liquid medium; 2) Insufficient suction head; 3) Blockage of the inlet and outlet pipes; 4) Foreign matter in the impeller; 5) Viscosity of the liquid exceeds the design index; 6) Wear of the ring; The prime mover is not spinning enough.
99. What are the obvious failures of centrifugal pumps?
Answer: 1) The pump can't start or the starting load is large; 2) the pump does not drain; 3) the pump is interrupted after draining; 4) the flow is insufficient; 5) the head is not enough; 6) the power consumption is high during operation; 7) the pump vibration or Abnormal sound; 8) bearing heat; 9) shaft seal heat; 10) rotor turbulence; 11) water hammer.
100. How to measure the sliding bearing clearance by the lifting shaft method?
Answer: Place the journal on the lower tile of the bearing, place a thousand gauge on the journal, and then lift the shaft to contact with the upper tile. The dial gauge difference is the bearing clearance.
101, what is the general content of the centrifugal pump minor repair?
Answer: Small repairs generally include: 1) checking the mechanical seal, cleaning the orifice plate on the flushing fluid line; 2) inspecting the bearing, cleaning the bearing housing; 3) eliminating leakage defects such as pump inlet and outlet lines, valves, flanges, etc.
102. What is the criteria for the rejection of ball bearings?
Answer: 1) Two raceway washers are stripped and severely worn. 2) The ball is broken or has pitting. 3) The cage is severely deformed and cannot be folded.
103. What is the criteria for the rejection of thrust bearings?
Answer: 1) When the thrust pad is seriously worn, its thickness is reduced by 1/2 or more; 2) When the thrust pad is melted; 3) The thrust pad is unshelled and cracked.
104. How to measure the clearance of rolling bearings with a feeler gauge?
Answer: Confirm the maximum load position of the rolling bearing. Insert the feeler gauge between the rolling element and the outer (inner) ring which is 180°. The thickness of the tightness is the radial clearance of the bearing. This method is widely used for self-aligning bearings and cylindrical roller bearings.
105, how to check the clearance of rolling bearings with a dial gauge?
Answer: Use a dial gauge to check, first zero the dial gauge, then push up the outer ring of the rolling bearing. The dial gauge reading is the radial clearance of the bearing.
106. How to check the rolling bearing when repairing the centrifugal pump?
Answer: 1) There should be no spots, holes, dents, peeling and peeling on the surface of the rolling elements and raceways; 2) The rotation is flexible, it should be stable after turning by hand, and it should be stopped gradually, and it cannot be stopped suddenly, and there is no vibration; 3) There should be a certain gap between the spacer and the inner and outer rings. The hand can be used to push the spacer test in the radial direction; 4) The clearance is suitable and meets the requirements.
107. What are the contents of the hydraulic turbine repair?
Answer: 1) including minor repairs; 2) inspection and replacement of mechanical seal components; 3) inspection and cleaning of mechanical seal flushing water lines, check valves, inlet filters.
108. Analyze from the equipment, how to extend the operating cycle of the single-stage centrifugal pump?
A; (1) The dimensions and shape tolerances of each part should be reduced as much as possible.
(2) The bearing clearance control is appropriate.
(3) The amount of mechanical seal compression should not be too large.
(4) The accuracy of the alignment should be improved.
(5) The spare pump is regularly driven.
109. What are the factors that affect the vibration value of the centrifugal pump?
A: Working conditions, load, assembly, alignment, foundation and takeover, pipeline stress, process operation.
Medical Coveralls,Surgical Coverall,Disposable Surgical Clothes,Medical Protective Clothing
Ningbo Autrends Prevention Products Co., Ltd , https://www.autrendsafety.com