If the wax pattern has defects such as pores, apex pits, live blocks not in place, and inclusions, it will affect the production progress, so it should be solved effectively and timely.
First, the defect description
The defect types and external features are as follows:
(1) On the partial surface of the stomata wax mold, a cavitation with a smooth surface is left, as shown in Fig. 1.
(2) The apex pit presents a pit on the wax mold corresponding to the ejector pin, as shown in Fig. 2.
(3) The live wax is not in place. The wax pattern and the live block correspond to the localized excess wax, as shown in Fig. 3.
(4) There are inclusions on the wax pattern of the inclusions, as shown in Fig. 4.
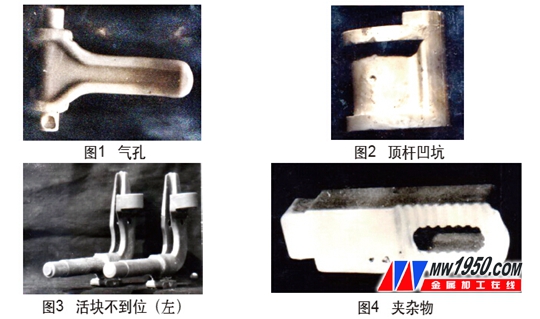
Second, the stomata
Cause
(1) In the production, the spiral blade stirrer is often used to stir the wax material. During the stirring process, a lot of gas is inevitably involved, and the key is that after the stirring, the wax material is not fully reprocessed, so that a large amount of the entrapped gas remains. In the wax.
(2) The position of the wax injection hole is set unreasonably, and the wax material generates eddy current during the process of injecting the pressure type cavity, and is entangled with the gas.
(3) Improper design of the press type is not conducive to cavity exhaust.
2. Preventive measures
(1) After the wax is stirred, it is subjected to a reductive treatment for a time of 0.5 h or more to sufficiently overflow the gas entrained in the wax.
(2) Improve the position of the wax injection hole to avoid eddy currents in the cavity.
(3) Improve the profile design to facilitate the discharge of gas in the cavity.
Third, the ejector pit
Cause
(1) In order to facilitate the mold release, the ejector is designed. When the ram is not reset in time, a ejector pit appears on the wax pattern.
(2) The wax mold is insufficiently cooled in the press type, and the surface hardness of the wax mold is low. At this time, the top rod is used for the mold, and the ejector pit is inevitably generated at the corresponding portion of the ejector rod.
(3) The cross-sectional area of ​​the ejector pin is small, and it is easy to appear the ejector pit on the corresponding surface of the wax mold.
2. Preventive measures
(1) Check the pressure before the combination, so that the ejector is in the normal position. If the ejector pin is not reset, it should be corrected in time.
(2) Prolong the cooling time of the wax mold in the molding and increase the hardness of the wax mold surface. However, it cannot be cooled for too long to prevent cracking of the wax pattern.
(3) Whenever possible, increase the cross-sectional area of ​​the ram to reduce the stress per unit area of ​​the wax mold.
Fourth, the live block is not in place
Cause
(1) When the mold is combined, the live block is not locked, causing the live block to shift when the wax is injected, and excess wax is present at the corresponding portion.
(2) The live block wears a lot after long-term use, so that it is not easy to be locked when it is combined.
(3) The pressure at the time of injection of the wax is too large to cause displacement of the living block.
2. Preventive measures
(1) When the mold is assembled, the block is locked so that it does not shift during the injection of the wax.
(2) The press type should be inspected before use and can be used for production after passing the test. When the live block is found to be worn, it should be repaired or replaced in time.
(3) Properly reduce the injection pressure to keep it within the normal range of use.
Five, inclusions
Cause
(1) Inclusions are mixed in the raw materials of the wax, or the wax is improperly stored in the inclusions.
(2) The working place between the molds is not clean, or the cavity is not cleaned when the mold is pressed, and the inclusions are left, and inclusions are generated during the wax mold making process.
(3) The viscosity of the top coat is too low, and the surface sand may penetrate the surface coating to enter the surface of the wax mold to cause inclusions.
(4) In the dewaxing process, the inclusions are easily mixed in the wax; the time of standing after dewaxing is too short.
(5) During the recovery process, the wax is allowed to stand for too short, so that the inclusions such as dust and sand are not precipitated or separated.
2. Preventive measures
(1) Strengthening the incoming inspection of wax raw materials, unqualified raw materials can not enter the factory; strengthen the storage of the warehouse to avoid the inclusion of inclusions in the raw materials of the wax; if necessary, it should be sealed and stored, or used for re-inspection during production, Qualified raw materials cannot be used for production.
(2) Always clean the mold room to keep it clean; clean the cavity before pressing the wax mold to keep it clean.
(3) Appropriately increase the viscosity of the surface coating, or reduce the sanding strength of the surface sand to ensure the quality of the surface layer of the shell.
(4) After dewaxing, it is allowed to stand for more than 2 hours, so that the inclusions in the wax liquid are effectively precipitated, and the dirt at the bottom of the dewaxing tank is cleaned in time.
(5) The recovered wax material should be allowed to stand for more than 2 hours, so that the inclusions in the wax liquid can be effectively submerged and separated; the cleaning wax liquid floating on the top is recovered, and the lower dirt is removed in time.
Sixth, wax mold process
The wax mold process parameters are shown in the attached table.
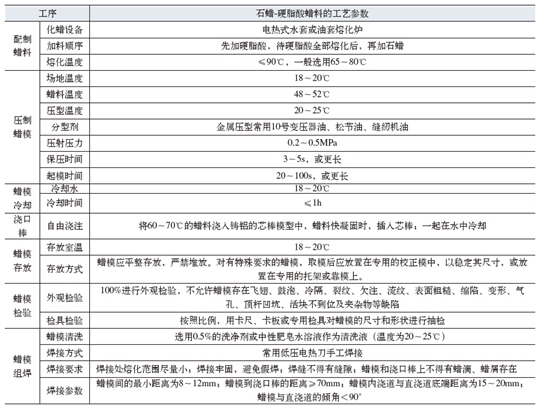
Conclusion
Making wax molds is an important process in investment casting production. The quality of wax molds directly affects the quality of castings. To this end, in the process of making wax molds, strict "three-press" (pattern, process and inspection standards), strict implementation of operating procedures, adhere to the "three inspections" (self-inspection, mutual inspection and special inspection), as long as they persist , can guarantee or improve the quality of the mold.
About the author: Pan Yuhong, Shenzhen Yingxun Precision Machinery Co., Ltd.
Ceiling Lamp ,Led Ceiling Light Fixture,Led Ceiling Lights For Living Room,Ceiling Mounted Light
Zhongshan Seekyo Lighting CO., Ltd. , https://www.seekyomodernlamp.com