Recently, our company has experienced batch quenching cracks in the heat treatment process of a certain part, and the scrapping rate is up to 20%. The material of the part is 27SiMn, and the heat treatment process is 480 ° C preheating (30 min) + (900 ± 10) ° C × 15 min salt bath heating cycle water cooling + 500 ° C tempering. In this paper, the physical and chemical analysis of the quenching crack causes of the parts is carried out, and a solution is proposed, which has achieved good results in the subsequent production.
1. Physical and chemical analysis
(1) Macroscopic observation As shown in Fig. 1, by observing the scrapped parts of the heat treatment, it is found that all the quenching cracks of the parts appear in or near the inner hole of the part. In the macroscopic state, the crack is radially along the inner hole of the part. The small zigzag extension, ranging from a few millimeters to a dozen millimeters, is 2 to 5 mm deep in the axial direction, and generally has several cracks per part.
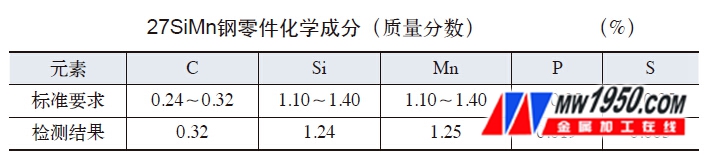
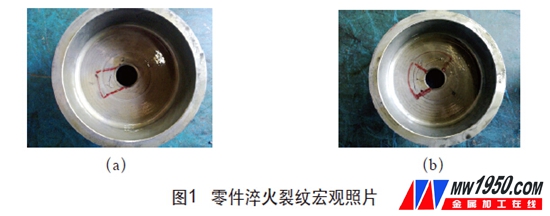
(2) Chemical composition test The cracked parts are sampled for chemical composition detection. The test results are shown in the attached table. The chemical composition is in accordance with GB/T3077-1999 "Chemical composition and mechanical properties of alloy structural steel".
(3) Metallographic analysis A sample was taken at the crack of the part for metallographic observation. As shown in Fig. 2, under the metallographic microscope, it is obvious that the crack extends along the grain boundary, and no decarburization and oxidation phenomenon is found on both sides of the crack. It should be a crack generated during quenching; crack cracking along the grain boundary It should belong to the crystal fracture; there are a large number of white network structures on the crack end and both sides, and the micro-hardness test is 312HV, which can be concluded that the white network is reticular ferrite. The inside of the grain is a tempered sorbite structure and a small amount of feathery upper bainite structure.
The metallographic observation was carried out on the core of the quenched part. As shown in Fig. 3, the matrix structure of the part was tempered sorbite structure + white reticular structure + a small amount of upper bainite structure. The micro-hardness test of the white reticular tissue has a microhardness value of about 300 HV, which can be judged as a reticular ferrite structure.
2. Discussion
In the quenched state of steel materials, there are generally two forms of ferrite structure.
The first form, quenching or normal temperature quenching heating in a sub-temperature state, but when the holding time is short, the ferrite structure is retained in the subsequent quenching cooling due to incomplete transformation into austenite or inability to change. The morphology is massive or semi-crescent in the grain boundary or inside the grain.
The second form, normal temperature quenching heating, but due to the slow cooling rate at high temperatures during cooling, the ferrite structure preferentially precipitates in the form of a network on the grain boundaries.
The difference in the form of ferrite structure in the matrix structure has a great influence on the properties of the material. In general, the first form has a good effect on relieving quenching stress, reducing quenching cracks, and improving low temperature brittleness, because the microstructure stress and phase transformation stress generated during martensitic transformation are due to ferrite structure. The good plasticity is greatly relieved, and the ferrite structure is distributed in the block or semi-crescent shape on the grain boundary, which can dissolve more trace elements such as S and P, and can eliminate reversible temper brittleness and improve steel. Cold and brittleness has a significant effect.
In the second form, since the ferrite structure is firstly deposited as a network along the grain boundary, the microstructure has a great influence on the mechanical properties of the steel, which greatly reduces the impact toughness of the material and increases the probability of occurrence of quenching cracks. The reason is that the ferrite structure is distributed in the grain boundary at the grain boundary. Due to the low strength of the ferrite structure, more trace elements can be solid-solved, which greatly weakens the grain boundary strength, reduces the impact toughness, and once the material is stressed. And the phase transformation stress is too large, the crack will preferentially nucleate at the grain boundary where the reticular ferrite is located, and crack along the grain boundary, causing a quality accident.
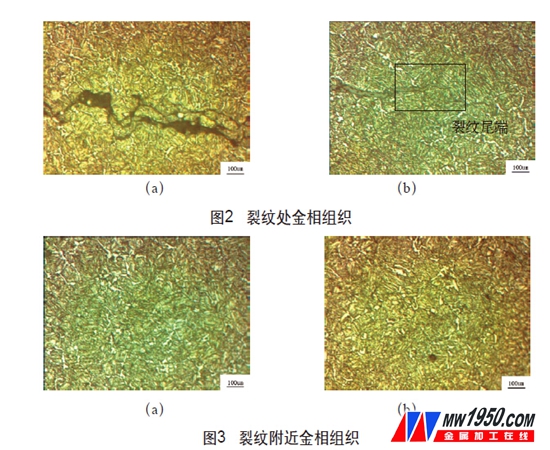
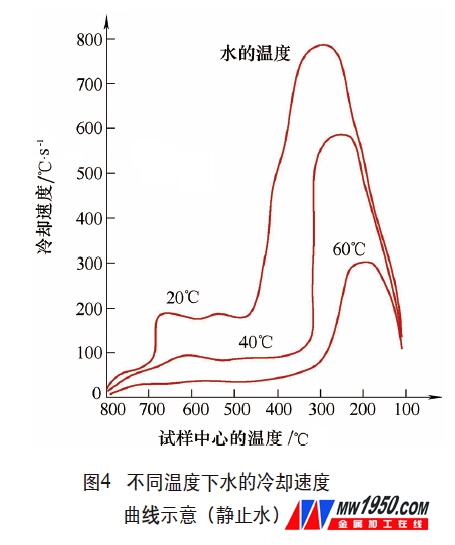
As described in the text, the cracked parts of the quenched parts appear at the inner holes. It can be clearly observed from the metallographic structure of the quenched part that there is a large amount of reticular ferrite structure, and the crack is cracked along the grain boundary, which indicates that the part has a problem in the quenching and cooling process. From the above physical and chemical testing, it can be seen that the carbon content of 27SiMn steel is upper limit, so the hardenability is better; in general, the critical diameter of 27SiMn steel can reach 38mm in 20 °C still water, and the effective thickness of the part is 13mm. Therefore, under normal conditions, the parts can be completely hardened in water, and the normal metallographic structure after heat treatment should be tempered sorbite structure, but the number of occurrences in the structure is observed from the metallographic structure of Figs. 2 and 3. More reticular ferrite structure and a small amount of upper bainite structure, this is not normal.
The quenching cooling medium of the part is recycled tap water. The cooling performance of water is very sensitive to temperature. When the water temperature is higher than 40 °C, the cooling performance will be greatly reduced. The cooling capacity in the high temperature zone (500-700 °C) will drop sharply, while in the low temperature martensitic transformation zone (200~). The low temperature cooling capacity of 350 ° C) is less reduced, as can be seen from Figure 4. The result of this is that the part is cooled slowly in the high temperature zone, causing the austenite structure to first transform into ferrite structure and distribute it in the form of a network on the grain boundary to weaken the grain boundary; in the low temperature zone, the cooling rate is too fast. Austenite transforms into martensite structure and the tissue stress is too large.
The author visited through the on-site investigation, the temperature control system of the salt bath furnace was normal, and the thermocouple detection accuracy was qualified. However, it was found that there were three problems in the heat treatment process of the parts: first, the quenching water tank door was damaged, and the circulating water of the quenching water tank was not well replaced. Second, the flow cooling water (higher water temperature) of the main electrode of the salt bath furnace flows directly into the quenching water tank, causing the water temperature of the quenching water tank to be higher; third, when the parts are actually quenched, the quenching interval of each furnace is shorter. And the volume of the sink is small, and the tap water in the sink is not updated in time. The above three factors lead to excessive water temperature during the quenching of the parts, reaching 50-60 °C. It can be concluded that the water temperature is too high, and the cooling performance of water in the high temperature zone of the part is greatly reduced. After the parts are quenched, the ferrite structure is distributed in the form of a network on the grain boundary, causing the grain boundary strength to drop sharply, while the low temperature cooling performance is The change is not large, resulting in too fast a rate of martensite transformation in the low temperature region, excessive tensile stress, crack cracking along the grain boundary.
In addition, the shape of the part and the quenching method also play a role in cracking the material. The shape of the part is more complicated, it is heated by a salt bath furnace, the quenching fixture passes through the inner hole, and the parts are vertically stacked, as shown in Fig. 5. The number of clamping parts per fixture is large, and the fixture is long. When the crane is quenched, due to the limitation of the speed of the crane, the fixture enters the water slowly when quenching the parts, so that the cooling speeds of the parts and the different parts of the individual parts are different; Since the quenching jig passes through the inner hole of the part, the inner hole is not smooth (the inner diameter of the part is 16 mm), causing the inner hole to cool slowly; and, as shown in Fig. 5, when the part is in the water, the position is 1 Cooling first, while position 2 causes the inner bore here and its position 3 to cool more slowly due to the air in its pocket.
The slow cooling of the inner hole leads to the easier precipitation of the reticular ferrite structure in the part, weakens the grain boundary, and also makes the residual thermal stress value generated by cooling in the high temperature zone relatively small, and in the low temperature martensitic transformation zone. The tissue stress generated by cooling is very large, and the superposition of the two causes a large tensile stress state on the surface of the inner hole. When the tensile stress exceeds the tensile strength, cracks are caused at the inner hole.
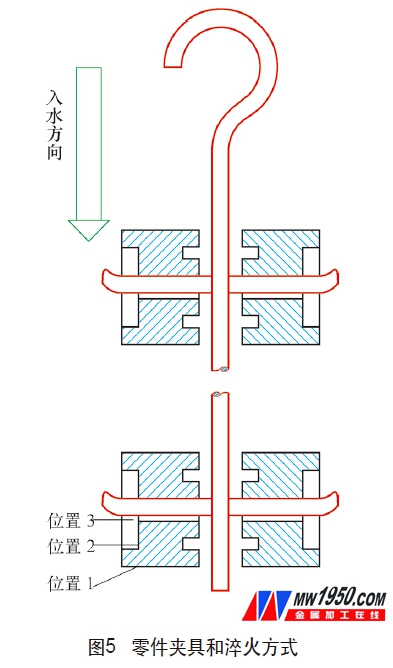
3. Conclusions and improvement measures
(1) The shape of the part and its quenching method cause the inner hole to have a slow cooling rate and a large tensile stress at the inner hole.
(2) During the quenching process, due to the damage of the quenching water tank valve, the water flow is not smooth, the water temperature rises, the cooling performance of the water is greatly reduced, and the ferrite structure is distributed in the form of a network on the grain boundary, causing crystal The boundary strength drops sharply, and under the residual tensile stress, an intergranular crack is formed.
In order to verify the above judgment, the author repaired the sink valve. In the next batch of trial production of the parts (the same batch of materials), the quenching water temperature was controlled within 30 °C, and the stirring force was increased. As a result, the quenching rate of the parts was greatly reduced and low. At 1‰, the correctness of the above judgment was verified.
About the author: Li Penghui, Lingyun Group Hebei Taihang Machinery Industry Co., Ltd. male, master, engineer.
Promotional Needles Cylinder Series
Needles Cylinder,Knitting Needles Cylinder,Circular Sock Machine Cylinders,Circular Machine Needle Cylinder
Changzhou Longfu Knitting Co., Ltd. , https://www.czcircularmachine.com