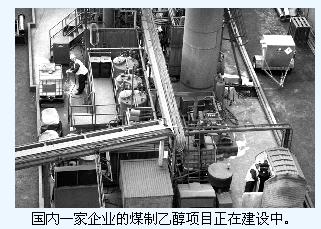
In September 2010, Henan Coal Chemical Group and the Chinese Academy of Sciences Biology Bureau and LanzaTech New Zealand signed an agreement in Zhengzhou to plan the use of coal gasification bio-fermentation to produce ethanol fuels and other chemical products for development and testing. Production and commercialization.
In January 2011, the global chemical giant Celanese announced that it had signed a letter of intent to build a new industrial ethanol plant in the Nanjing Chemical Park and Gaolan Port Economic Zone in Zhuhai. The initial rated capacity of the single plant is 400,000 tons per year. The initial investment of the factory is about 300 million U.S. dollars. In June 2011, Celanese announced that in addition to the original investment plan, it intends to use its advanced ethanol production technology to improve the existing coal chemical integrated plant located in Nanjing Chemical Industry Park. If approved by the government, the improved plant can increase production capacity of approximately 200,000 tons of industrial ethanol by mid-2013. Celanese said that the technology developed by the company can produce industrial grade and fuel grade ethanol.
According to the CCIN reporter, the Jiangsu Industrial Thorpe (Group) Co., Ltd. is currently constructing an industrial demonstration plant that uses syngas to produce 10,000 tons/year of ethanol. In addition, Yankuang Group is also advancing cooperation in syngas bio-based ethanol production technology to prepare 300 tons/year coal-to-ethanol pilot plant.
In addition to chemical companies, there are also some outside companies that are conducting this business. In March 2011, the 300-ton/year tail gas ethanol production demonstration project of Baosteel Group, New Zealand's Lanze Company and the Chinese Academy of Sciences began construction in Shanghai. The project plans to use the tail gas (mainly carbon monoxide) produced by the steelmaking plant, adopt the Langze company's bio-fermentation technology to make ethanol, and combine with the membrane separation technology and fermentation process of the Chinese Academy of Sciences. The project construction period is expected to be 6 months. Once the demonstration project is completed, the parties will start the commercial scale ethanol plant project in due course.
For this wave of coal-to-ethanol development boom, people can not but ask three questions.
One question: Can technology pass?
Tang Hongqing, senior engineer of China National Synthetic Oil Engineering Co., Ltd., told CCIN that the process routes for coal-to-ethanol production are mainly divided into three types: first, direct synthesis of syngas to ethanol; and second, syngas bio-based production of ethanol, ie, the use of microbial fermentation technology. Syngas (including exhaust gas containing carbon monoxide and hydrogen) produces ethanol; third, synthesis gas is hydrogenated to produce ethanol.
So, are these three technologies mature? CCIN reporter found in the survey interview that the industry's views on this are not consistent.
Tang Hongqing told CCIN reporter that syngas bio-processes ethanol, because the fermentation needs to stay for a period of time, so it is difficult to continuous production, the cost will not be low; syngas directly to ethanol, a long process route, and the current world's catalysts are not yet After clearance, the product comes out of a mixture and needs to be purified. He believes that in the coal-to-ethanol route, the route to hydrogenation of syngas to ethanol via acetic acid is the most promising and the cost may be the lowest. According to him, hydrogenation of acetic acid to ethanol, in theory, consumes 1.304 tons of acetic acid and 973 cubic meters of hydrogen per ton of ethanol, yielding 391 kilograms of water. At present, acetic acid is cheap, and acetic acid production technology is mature. Therefore, ethanol production by hydrogenation of acetic acid is expected to be large-scale and large-scale.
He Yongde, a coal chemical expert and a member of the expert group of the Shaanxi Provincial Decision-making Advisory Committee, holds another view. He said that if ethanol is used to hydrogenate acetic acid, this technology line will be competitive only if the price of acetic acid is below 4,000 yuan/ton. He believes that this route is mainly to solve the problem of excess domestic production of acetic acid. If the price of acetic acid exceeds 6,000 yuan/ton, this route will be completely uncompetitive. He also believes that acetic acid is produced by the carbonylation of methanol and carbon monoxide, while methanol is synthesized by hydrogen and carbon monoxide. Originally, hydrogen and carbon monoxide synthesis can directly produce ethanol. If it is used to produce acetic acid and then hydrogenate to ethanol, it is equal to return from the production process. There are many bends around, and the energy efficiency becomes low and undesirable. Therefore, he believes that the syngas synthesis of ethanol is the most promising and it is easy to scale.
According to Jin Yong, an academician of the Chinese Academy of Engineering and a professor at Tsinghua University, the reaction of ethanol production by biological fermentation is relatively slow and there are problems in the amplification.
From the above perspectives, it can be seen that although the opinions of experts are not consistent, the current three types of coal-to-ethanol routes have their own disadvantages and bottlenecks. This also shows that the current coal-to-ethanol technology is still immature, because after all, there are no industrial devices yet, and it will take time and practice to test it.
Second question: What is the cost?
What about the cost of producing ethanol from coal compared to the previous ethanol route?
He Yongde told the CCIN reporter that using coal to make ethanol requires 5,000 cubic meters of syngas to produce 1 ton of ethanol, and the estimated cost of coal to ethanol is around 4,000 yuan per ton.
Zhang Zhiwei, deputy chief engineer of Yantai Guotai Chemical Co., Ltd., said that at present, China mainly adopts traditional grain fermentation to make ethanol, and the market price has reached 7,000 yuan/ton. At present, domestic cellulosic ethanol is still in the pilot stage, according to the public data of various companies, the cost is 7000 ~ 8000 yuan / ton. If the cost of coal-to-ethanol production can be maintained at 4,000 yuan/ton, this is lower than the cost of grain ethanol and cellulosic ethanol.
According to the CCIN reporter, the largest downstream market for ethanol is currently blended with gasoline to form vehicle fuel, namely ethanol gasoline. So is coal-to-ethanol competitive in cost compared to methanol fuel, which is also a new type of automotive fuel and is also produced from coal?
"Coal-based ethanol is useful as a fuel, but it has no cost advantage over methanol fuel." Fang Dechen, vice president and director of the technical committee of the national alcohol ether fuel and alcohol ether cleaning professional committee, told CCIN reporters. According to him, according to the chemical reaction, 64 tons of synthesis gas produced 46 tons of ethanol and 18 tons of water, that is, 1.4 tons of synthesis gas produced 1 ton of ethanol, and the conversion rate of synthesis gas was 71%. The coal-to-methanol is basically converted from 1 ton of synthesis gas to 1 ton of methanol, and the conversion rate is close to 100%. In addition, the by-product of coal-to-ethanol is water, and 1/4 of the hydrogen in the syngas is lost. However, the by-product of coal-to-methanol is less and the loss is very small. Moreover, syngas to ethanol is technically more difficult than methanol, the product components are also more complex, crude products also need hydrogenation and refining treatment, the catalyst costs are high, but also a big expense.
He Yongde further told CCIN reporters that the full cost of producing methanol from coal to syngas is 2,000 to 2,500 yuan per ton, and coal to ethanol is estimated to be around 4,000 yuan per ton. The cost of coal-to-ethanol production is nearly half that of methanol, so there is absolutely no competitive advantage. If coke oven gas is also used to produce ethanol and methanol, the production cost of ethanol is also higher than that of methanol. Now the price of coke oven gas is also rising. If the price of coke oven gas is 0.5 yuan/m3, the ethanol produced will cost 1,000 yuan more than the cost per ton of methanol.
Three questions: Can the downstream be opened?
Some experts believe that coal-to-ethanol is feasible as a chemical raw material.
Fang Dexi said that ethanol is not only a good solvent, but also can be used as a raw material for a variety of chemical products. He said that coal-to-ethanol can be used in the future instead of ethanol for food fermentation to produce downstream chemical products.
According to CCIN reporters, some companies intend to practice this. For example, the person in charge of Jiangsu Thorpe (Group) Co., Ltd. stated that the use of coal to ethanol will be used to synthesize ethyl acetate. Celanese also announced that it will prioritize industrial-scale applications of coal-based ethanol products.
According to insiders, China currently consumes about 3 million tons of industrial-grade ethanol each year. The ethyl acetate production capacity in China alone has reached about 2 million tons, and the amount of ethanol consumed is 1.2 million tons. The production of downstream chemical products from coal to ethanol not only reduces production costs, but also greatly reduces dependence on grain ethanol. Zheng Baoshan, senior engineer at the Institute of Petroleum and Chemical Industry Planning, said that if coal-to-ethanol can be successfully produced, acetic acid companies can also dehydrate ethanol to produce ethylene and develop ethylene-vinyl alcohol resins that have great market potential in China.
So, can the coal-to-ethanol market for automotive fuels be opened?
Some experts are pessimistic about this issue.
Xiao Mingsong, secretary general of the China Rural Energy Industry Association's Biomass Professional Committee, told CCIN reporters that the biggest difference between coal-to-ethanol and cellulosic ethanol is that coal is non-renewable and will be used less and less, while cellulose (such as straw Etc) is renewable. In contrast, cellulosic ethanol has better policy support than coal-to-ethanol.
Feng Wensheng, a senior engineer of Henan Tianguan Enterprise Group Co., Ltd., which is one of the four designated fuel ethanol production enterprises approved by the National Development and Reform Commission, believes that coal-to-ethanol is more difficult to approve than biomass-based ethanol, and is also more complicated. In addition, coal-to-ethanol is also relatively more polluting than biomass, and it is difficult to pass the first environmental assessment.
Tang Hongqing stated that after the coal-to-ethanol production, the specifications of the food law are different. Studies in other countries have shown that half of coal-based ethanol is methanol, as well as trace components such as tri-carbon compounds, tetra-carbon compounds, and penta-carbon compounds. Whether these ingredients can be added to gasoline or negotiated with car fuel dealers requires a lot of procedures. This is a very troublesome task.
However, Jin Yong believes that coal-to-ethanol is a new direction for the development of the new coal chemical industry. If coal-based ethanol meets the purity requirements as a fuel, the production capacity will reach millions of tons. There will be no resistance in PetroChina and Sinopec. Reason for blocking.
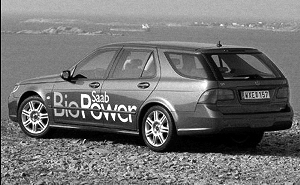
The picture shows an ethanol car developed by a foreign company.
Elevator Rope Attachment with spring, Elevator Rope Attachment with rubber, Elevator Wedge Socket, Elevator Rope Fastening
OTIS Elevator Rope Fastening, Thyssen Elevator Rope Fastening, KONE Elevator Rope Fastening, GiantKONE Elevator Rope Fastening, ThyssenKrupp Elevator Rope Fastening, Schindler Elevator Rope Fastening, XJ Schindler Elevator Rope Fastening, Xizi OTIS Elevator Rope Fastening, Mitsubishi Elevator Rope Fastening, Shanghai Mitsubishi Elevator Rope Fastening, Fujitec Elevator Rope Fastening, Hitachi Elevator Rope Fastening, Toshiba Elevator Rope Fastening, Hyundai Elevator Rope Fastening, LG Elevator Rope Fastening, Sigma Elevator Rope Fastening, Express Elevator Rope Fastening, GUANGRI Elevator Rope Fastening, FUJI Elevator Rope Fastening, BLT Elevator Rope Fastening, CANNY Elevator Rope Fastening, SJEC Elevator Rope Fastening, KOYO Elevator Rope Fastening, IFE Elevator Rope Fastening
Elevator Rope Fastening,Elevator Steel Wire Rope Fasteners,Elevator Rope Fastener, Elevator Rope Attachment, Elevator Wedge Socket
CEP Elevator Products ( China ) Co., Ltd. , https://www.zjelevatorcontrolsystem.com