The GM223 type tube mill pinion seat of the alumina branch of Chinalco Shanxi Branch is made of HT15233. During the use, the bottom plate of the four feet of the bottom plate is broken and one crack occurs. Since it takes at least three months to reorder, and the production situation is relatively tight, the tube mill is required to be used as soon as possible, so it is decided to weld the pinion holder.
1 Defect situation and failure analysis
1.1 Fracture of the pinion seat
There are two breaks in the four screw holes of the pinion base plate (in the pinion seat and 1). There are two breaks in the bottom plate. The position and the beginning of the split are shown in Figure 1, Figure 2. The block size is 270 mm × 250 mm × 70 mm. The fracture size is 270 mm × (100 mm to 130 mm).
2) The bottom plate is broken, as shown in Figure 1, which has been cracked.
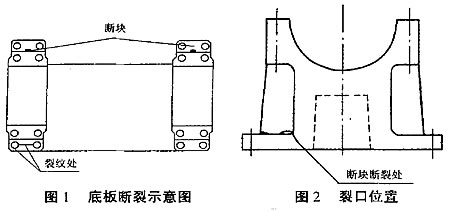
1.2 Failure Analysis
The pinion seat itself is more restrained in use. It is subjected to alternating load during the operation of the tube mill. There is a manufacturing defect in the workpiece itself, and there is stress concentration at the edge of the rib joint with the bottom plate. During operation, due to the large restraint and alternating load, the prestressed stress is destroyed, cracks are formed, and the crack is gradually extended to the ribs.
2 repair options
According to the current state of the art, the manual arc welding method is used for repair.
2.1 Technical performance parameters of materials
1) The chemical composition of HT15233 is shown in Table 1.
1 Chemical composition%

2) The performance parameters of HT15233r are shown in Table 2.
2 performance parameters

2.2 Analysis of weldability of iron
Due to the inherent properties and metallurgical properties of cast iron, it has brought great difficulties to arc welding, as follows:
1) After melting, the cast iron has a fast cooling rate, and the white-mouth structure tends to appear in the heat-affected zone, and the cracking tendency tends to be large during welding.
2) Among the components of cast iron, the carbon content is high, and carbon is easily vaporized during the welding process, and pores are easily generated.
3) Cast iron has high strength, poor plasticity, and large residual stress during welding, which is prone to weld hot cracks.
4) The content of C, S, P and other elements in cast iron is high, and it melts into the weld during the welding process, which increases the hardness of the metal, reduces the plasticity and toughness, is prone to cracks, and reduces the workability.
5) During the smelting process of cast iron, graphite coarsening is likely to occur, and the gap between graphite and matrix causes the oil and water to penetrate into the oxide during the use of the casting, which seriously hinders the fusion during welding and increases the possibility of welding cracks and pores. Sex.
6) When the cast iron is welded and melted, the liquid metal has poor fluidity, which seriously hinders the fusion during welding. The molten slag and harmful gases in the molten pool are difficult to escape, which may cause serious defects in the weld.
In view of the above disadvantages, it must be solved from the aspects of welding process, operation method, welding procedure and welding material.
2.3 Selection of welding methods
Manual welding of cast iron can be done by heat welding and cold welding. Manual arc heat welding is to start the welding of the whole workpiece to 600 ° C ~ 650 ° C or above. The working temperature during the welding process must not be lower than 400 ° C, and immediately after welding to 650 ° C to eliminate stress annealing.
The weight of the pinion seat is 1.74 t, and the alumina plant does not have suitable heating equipment, so it is repaired by manual arc cold welding. The cold welding method refers to welding by a welding method that does not preheat and strictly controls the interlayer temperature and the small line energy.
2.4 Selection of welding materials
The weldability of HT15233 is poor and the lower surface of the base is the machined surface. To ensure the welding quality and the workability of the lower surface, it is better to use pure nickel-based electrode Z308 for welding. However, Z308 electrode is expensive, in order to save cost, it can be repaired by Z308 welding strip insulation layer, J507 welding rod and Z308 welding rod filling each other, Z308 welding rod cover surface, which can reduce the cost and ensure the welding quality and the lower surface. Machinability.
The mechanical properties of the Z308 electrode are shown in Table 3.

2. 5 welding order
1) The cracks are applied in the order of the non-machined surface reworked surface.
2) At the broken block, first weld the side of the rib to ensure penetration, and then clean the root and weld from the other side. After welding the ribs.
3 welding
Thoroughly clean all welded parts before welding to remove all defects such as crusting and oil, and then start welding preparation.
3.1 Welding preparation at the crack
After the surface is cleaned, use a corner polisher to grind the crack to the desired double U-groove. It is required to eliminate all cracking tendency during grinding, and the edge of the groove is smoothly transitioned. The blunt edge and the gap are subject to unilateral penetration.
3.2 Welding preparation at the block
The shape of the two fault blocks is basically regular. After the surface is cleaned, the angle is polished to a double U-shaped groove according to the required shape and size of the groove. The blunt edge and the gap can be welded by one side and the other side. The side is based on the root, and then the block and the pinion seat body are paired and fixed on the scribing platform according to the size.
3. 3 welding
The pinion seat has a large amount of welding and welding. In order to reduce the welding stress and welding deformation and ensure the welding quality, a two-shift system is adopted to fix the high-level welder. The ambient temperature during welding is guaranteed to be above 20 °C, and if the temperature is too low during night shifts, the welding is stopped. In order to prevent the wind from entering the temple, an awning is set up during welding to prevent wind insulation. Weld the crack first, then weld the broken piece. When the crack is welded, the crack in the middle of the two screw holes is welded first, and the outer crack is welded after the welding.
1) Before welding, Z308 electrode should be dried at 150 °C for 1 h, J507 should be dried at 250 °C for 2 h, dried and placed in a heat preservation bucket for heat preservation.
2) Place the weld bead in a horizontal position for each weld to facilitate operation.
3) Short-circuit, fast, non-winding, intermittent, and dispersive welding methods are used for welding. The length of each section is not more than 30 mm, and the arc pit should be filled when the arc is closed.
4) Immediately after welding, hammer the entire weld bead with a blunt-headed hammer to release the welding stress. The hammering speed is faster and the force is gradually lighter.
5) Strictly control the interlayer temperature, and each welding must be cooled to below 50 °C to continue welding.
6) When the base is used, the welding is performed with a small fusion ratio, and the fusion ratio and the surface welding can be appropriately enlarged.
7) After removing the slag, observe with a five-fold magnifying glass, no cracks, and then continue the next welding.
With the development of construction, automobile, decoration, furniture, information technology and other industries and the improvement of people's requirements for living space environment, functional processing products such as safety vacuum glass and Energy Saving Vacuum Glass have been widely used. The supply and demand pattern and consumption structure of vacuum glass are changing. The internal of ICESUN vacuum glass is in a vacuum state, which is not affected by the ambient air pressure and is suitable for various altitude areas. That means the application of Vacuum Glass For Buildings in all positions of buildings can maintain its excellent performance, including facade, slope and roof. There is no problem that the performance of tempered vacuum glass would be reduced due to the increase of gas convection when the hollow glass is placed horizontally. Therefore, energy saving vacuum glass is the best choice as building glass for ultra-low energy consumption buildings.
Safety Vacuum Glass,Safety Vacuum Composite Glass,Safety Vacuum Laminated Glass,Safety Tempered Vacuum Glass
ICESUN VACUUM GLASS LTD. , https://www.icesunvacuumglass.com