Abstract [Background] On October 19-24, 2015, according to the annual key work arrangement of the Cross-Strait Entrepreneur Summit, Chen Huiren, executive vice president and secretary general of China Machine Tool Industry Association, led a delegation to Taiwan to conduct peer-to-peer exchange activities. &n
ã€background】 On October 19-24, 2015, according to the annual key work arrangement of the Cross-Strait Entrepreneur Summit, Chen Huiren, executive vice president and secretary general of China Machine Tool Industry Association, led a delegation to Taiwan to conduct peer-to-peer exchange activities.
During his stay in Taiwan, the delegation concentrated on the Precision Machinery Research and Development Center, Yongjin Machinery Industry Company, Suichang Electromechanical Company, Qinghong Electromechanical Industry Company, Taiwan Yinxing Co., Ltd. and Yintai Technology Co., Ltd. in Taichung. The main business involves application technology research, machining centers, electric machining machines, spindle motors, internal and external protection devices and rolling functional components. These six companies are typical representatives in the field in Taiwan or in the top three, and the types are more comprehensive: there are both production enterprises and scientific research institutions; in the enterprise, there are both host enterprises and The functional component supporting enterprise; in the host enterprise, there are both the gold cutting processing host enterprise and the electric processing host enterprise.
Therefore, this inspection activity is very helpful for understanding the overall situation of the Taiwan machine tool industry, and has thus formed a series of investigation reports to share with the industry.
The visit of Taiwan Xingxing Co., Ltd. (hereinafter referred to as the Xingxing Company) was the most exciting and experienced stop for the visit, especially the company's unique corporate culture left a deep impression on everyone.
The company was founded in 1983. Its main products include internal and external protective devices and chip removal mechanisms. Although the product is not a major component of the machine tool, and there is not even a high technical content, the company has made such a small business into a big business. The company’s sales revenue in Taiwan has reached NT$1 billion (equivalent to In the RMB 200 million yuan, it accounts for more than 75% of Taiwan's market. The company not only built a new Kaohsiung branch in Taiwan, but also established Shanghai, Jiaxing and Kunming branches in the mainland, and Shenyang Branch is also under construction. The high-speed protection device of the company has a good reputation in the mainland.
Behind the impressive achievements, Wang Qinghua, the founder and chairman of the company, has been tirelessly exploring and pursuing for a long time in corporate management and cultural construction. They have made the product to the extreme, the cost has been reduced to the extreme, and the cultivation of employees has been achieved to the extreme.
Compressing inventory to almost zero The most direct example of managing a company's benefits is the relentless pursuit of production processes and inventory compression. Before 2007, the entire production cycle from feeding to packaging was 7-10 days, the production line was 88 meters long, and each production line was 7 people; the production cycle is now 4 hours, the production line is 20 meters long, and each production line is 4 people. This is already a very advanced level, but the company is currently undergoing a reorganization of the production process, the production cycle will be compressed to 30 minutes, 2 people per production line. In this process, the production area is also correspondingly greatly compressed. It’s incredible!
Corresponding to the shortening of the production cycle is the compression of inventory and warehouse area. According to Chairman Wang Qinghua, since 2007, the company's in-process and finished goods inventory has never exceeded 0.6% of annual operating income (the average level of Taiwan's machinery manufacturing industry is 20%), close to zero inventory. We saw in the workshop that the connection between the processes was very good and there was almost no work in progress. What is even more surprising is that the so-called finished product library is the two rows of squares painted on the ground at the exit of the workshop. When we visited, the goods just arrived, and the finished product warehouse was completely emptied.
The area of ​​the original auxiliary materials library of the company is much smaller than that of the general enterprises. The main raw material steel plate, the quantity of one-time purchase is two days of production, and the standard quantity of screw nut and other standard parts is 7 days.
Induction of the company's internal zero inventory and on-time production, but also extended to users. They real-time bus delivery, that is, according to the user's location, 9 fixed routes are planned, and they are delivered once every half hour. According to the user's production plan, the products needed for the day are directly sent to the user's production line. To achieve the above, the production plan of the company must be very detailed, and it is closely linked with the production plans of the original auxiliary materials suppliers and user companies.
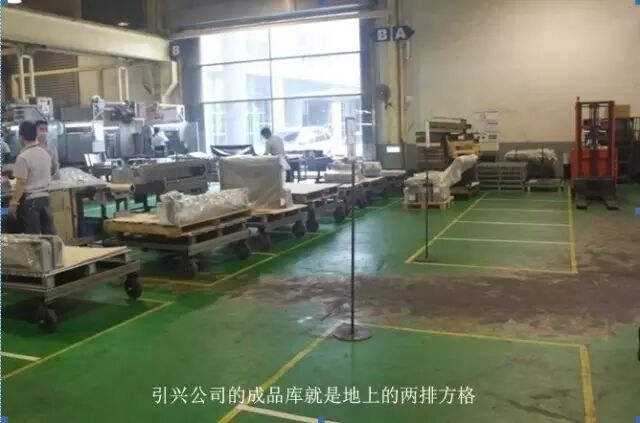
The normalization of management norms is one of the highlights and features of the management of the company. All management practices must be maintained at all times and are not allowed to be provisionally organized. We looked down from the second floor corridor of the workshop to the whole workshop. Every production line and each station where we were nervously produced were very neat and tidy.
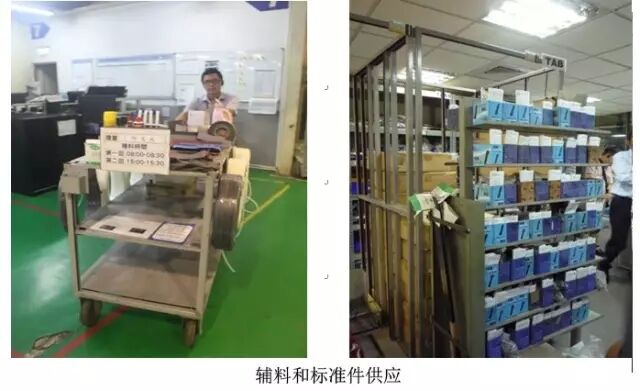
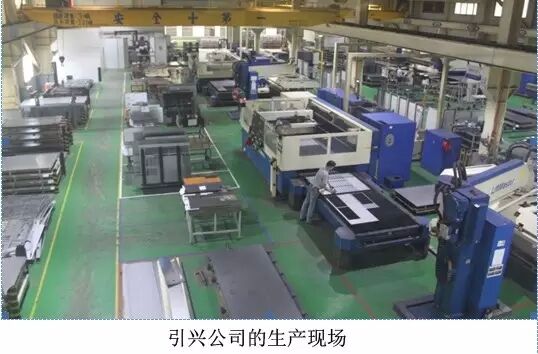
The company has an area of ​​only 5,000 square meters, but the building area is more than 10,000 square meters. The company's use of the area has reached a point where it must be compared. Not only the area of ​​each production line and each station is repeatedly compressed, but the area occupied by office and warehouse is also unimaginable. Even the stairs of the office building are steep. It is also very large, using steel plate welding, so that the area occupied by the stairs is significantly compressed.
The standard, fine and humane corporate culture attracts the management of the company so finely that it is impossible to have high recognition and conscious action by all employees. Therefore, the company has cultivated a very unique corporate culture for a long time. Its basic characteristics are: standardization, refinement and humanization. Regardless of the job, the employee's salary and benefits, everything has standards, and there are behavioral norms for all the details of everything. For example, if something goes into the conference room, you can't knock on the door, so as not to interfere with the meeting. Instead, you should write a good note and walk quietly to the leader to hand it to the leader. Another example is the meal: the rice bowl should be placed outside the rice bowl to avoid something falling into the rice bucket; the rice is full of eight minutes; if the rice is falling, use a napkin to clean it;
Of particular note is the regulations on the bathroom. There are 16 toilets in the headquarters of the company, and there are no cleaning staff, but they can keep them clean at all times. The reason is very simple, that is, each user needs to be restored to a clean state after using it.
In terms of etiquette and interpersonal relationships, the company has high requirements for employees. Colleagues' greetings, phone calls, handshakes, directions, etc., are all detailed. For example, colleagues meet early in the morning and go to work in the morning to see each other. When smiling, the eyes smile first, the corners of the mouth are U-shaped, revealing 8 teeth; the registration room registration must not allow guests to fill in the bill; the elevator and dining guests are preferred;
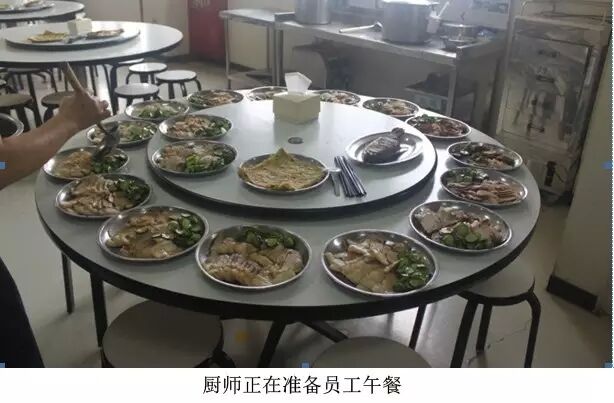
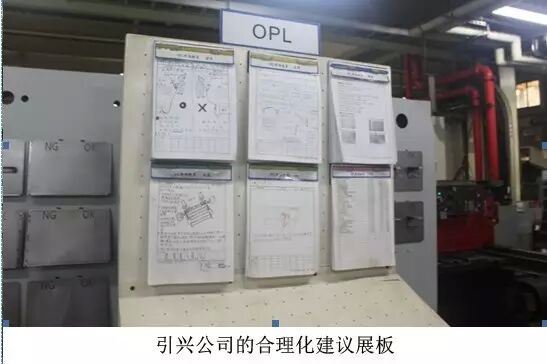
The company provides free three-day meals for employees, and the standard is not low, but the rice bowl needs to be prepared by employees according to the size given by the company. The implication is: the rice bowl is its own, we must cherish the job opportunities. Good intentions can be described as good.
I visited the scene of the company and listened to the introduction of Chairman Wang Qinghua on corporate management and corporate culture. Everyone was deeply touched and got a lot of useful inspirations. In the past, we often thought that corporate culture was relatively imaginary, and often labeled corporate culture as a slogan. The example of the company is that the corporate culture is to use a detailed code of conduct to tell employees: how to talk, how to do things, how to behave in this company. It is very specific and very real, but these are essential elements for producing quality products and are closely related to the business results of the company.
The company is not a big company in Taiwan, but it is definitely a company with excellent management and successful operations. This seems to be proved when Ma Yingjiu attended the ribbon-cutting ceremony when the company's new office building was completed. Nowadays, many companies in Taiwan want to introduce the management model of the company, and the company has established a management consulting company for this purpose.
China leading manufacturers and suppliers of Polyacrylamide Water Treatment,Cationic Polyacrylamide Flocculant, and we are specialize in Polyacrylamide Soil Conditioner,Poly Aluminium Chloride For Drinking Water, etc.
Polyacrylamide Water Treatment,Poly Aluminium Chloride In Wastewater Treatment,Poly Ferric Sulfate Water Treatment,Aluminium Sulfate Flocculation
Shaanxi United Xingchuang International Co., Ltd. , https://www.lxcgj.com